Common Causes of Deviations in the Pharmaceutical Industry
Process deviations in manufacturing are unavoidable, yet controllable, problems that pharmaceutical companies must account for during production timelines. Even small variations early on in the process can result in significant problems downstream, which can lead to defective products, setbacks during release, and medical regulations violations.
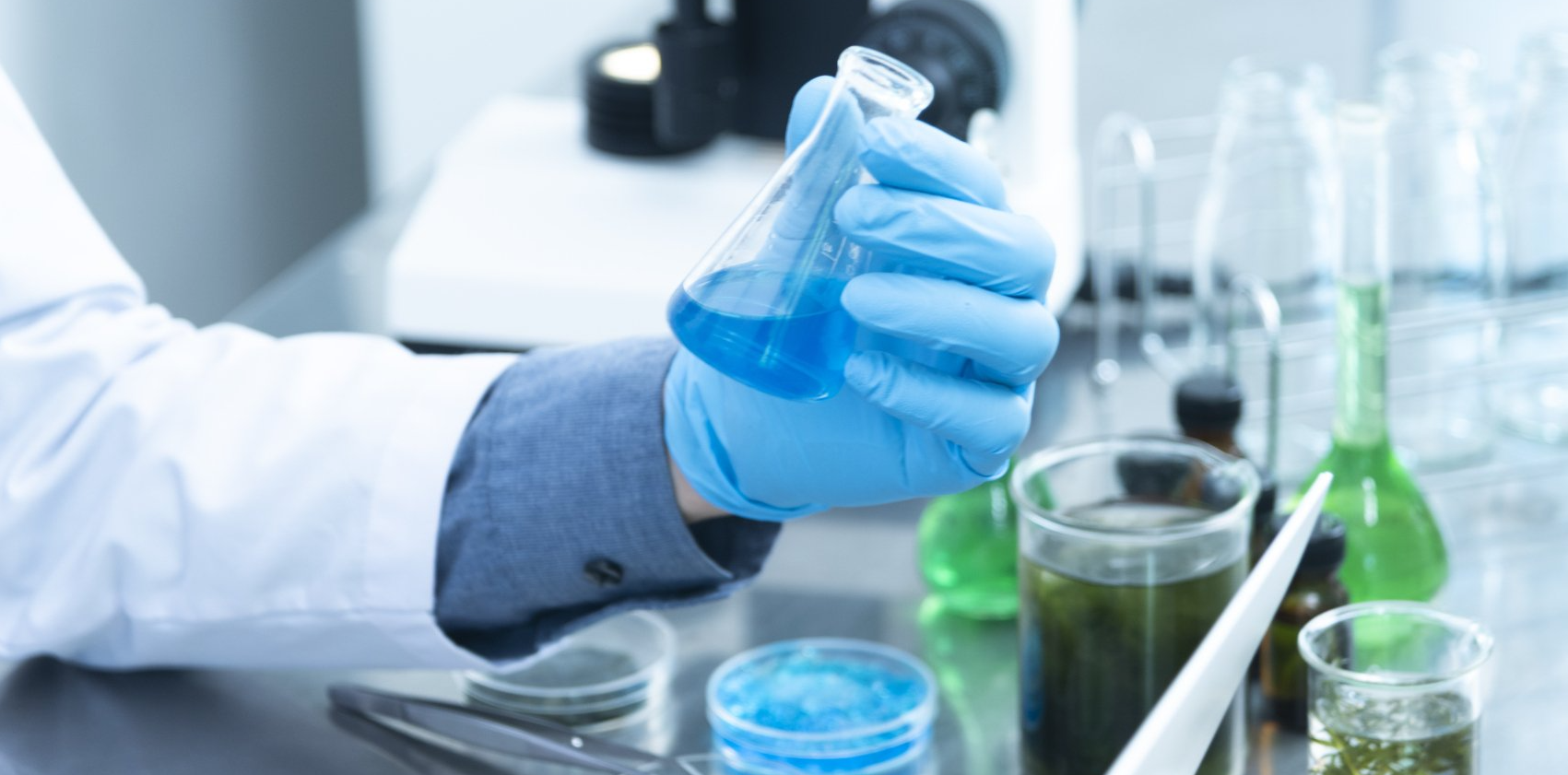
No matter how well-documented and controlled your pharma manufacturing process is, deviation management will always be a necessity. In order to protect the health and safety of their patients and reputation in the medical industry, pharmaceutical manufacturers must understand where deviations come from and how they impact product quality.
FDA Rulings on Deviation in the Pharmaceutical Industry
In the past, facilities only had to collect metrics on the first three batches and the end product to receive validation. But 2011 marked a major shift in the way the U.S. Food and Drug Administration handled deviations in pharma.
The key term to know is “continuous process manufacturing,” which the FDA installed after receiving product recalls and complaints for otherwise “validated” products. This mandate requires that manufacturers adopt a continuous process control to monitor their performance, rather than at specific points. Consult the FDA’s official guide on continuous process validation for more information.
Common Sources of Process Deviations
It isn’t sufficient to simply know what deviation is in pharma; medical facilities must be aware of the types of deviation or the true root causes for why the planned process could go awry to some extent.
- Contamination: Possibly the most well-known issue that arises in drug production is impurities and contamination by microorganisms or viruses. Microbiological root cause analysis data can help identify the contaminants.
- Equipment: Equipment failure can always occur in any setting with machinery and moving parts. Mis-calibrated sensors also pose a threat to the quality of medical devices coming out of the factory. Predictive maintenance is the best defense to avoid process issues.
- Human error: The staff on the factory floor are often a weak link in the production chain. For example, carelessness or genuine mistakes can result in cleaning procedures not being fully followed. Human error is a diminishing concern thanks to automation, but you can reduce its incidence further by providing machinery operators proper training and oversight.
- Process controls: Disruptions in production, such as those caused by equipment failure, and unknown variables impacting standard procedures can each generate deviations. Controlling processes starts with data and metrics, and most businesses rely on multivariate data analysis to check for deviations.
- Raw materials: Perhaps the issue isn’t within your facility at all, but rather coming from external suppliers. Whether there’s a defect with the raw materials themselves or the vendor contaminated them in transit, screening your materials beforehand prevents these defects from impacting the quality of your final product.
It’s worth noting that Good Manufacturing Practices set by the FDA considers all deviations to be unplanned. However, a term exists known as “planned deviation” which refers to temporary changes in the production process that have been pre-approved for a certain period.
What Often Causes Those Deviations?
One of the challenges to addressing process deviations in pharmaceutical companies is that the typical approach, deviation investigations, often skips the details and results in a failed attempt to grasp what truly is wrong with the process. For example:
- Production processes are poorly defined by the research and development team before being sent to the facilities.
- Collecting accurate information required for production is delayed, resulting in an uninformed process.
- During a typical deviation investigation, the actual problem is not discovered. Auditors may instead find a symptom rather than a true cause.
- Performance metrics and deviation reports are not recorded and presented properly, leaving management in the dark about what’s going on.
- Roles are not properly defined, so those responsible for deviations are never held accountable, and auditors will often notate deviations without any action by management being taken.
- The business in general fails to see deviations as a threat or does not take any corrective action, even as repeat problems occur as a result.
Many of these types of errors in pharmaceutical analysis are actually addressed directly in the FDA’s 2011 ruling on continuous process validation mentioned above. Once a company takes on a culture of analysis and continuous improvement, deviations become much less of a hassle.
Understanding CAPA Root Cause Analysis
Let’s end our discussion with a rundown of Corrective and Preventive Action (CAPA). The FDA requires that medical manufacturers adopt this practice as part of a root cause analysis.
Imagine you work for a medical device production facility. When a deviation causes a noticeable issue in the final product, that deviation triggers a chain of events and symptoms that ultimately leads to a faulty device or presents a potential risk to public health. The next step is to determine exactly what that initial deviation was through a root cause analysis.
Not only can you improve the quality of your output through CAPA, but it can also help prevent problems down the line and give you valuable insights into improving the continuous manufacturing process.
Because a root cause analysis is heavily data-driven, you will be seeing a lot of scatter plots, flow charts, and other tools on your journey to learning exactly “why” a problem first developed.
CfPIE Gives You the Training You Need To Address Pharma Deviations
CAPA, root cause analysis, and other methods to address deviations in medical manufacturing are far more complicated than can be explained in this article. If you’re interested in getting your company up-to-date with the latest best practices for addressing pharma deviations; begin your proactive approach to continuous quality improvement by getting in touch with CfPIE and reviewing our training course on Pharmaceutical Root Cause Analysis of Failures & Deviations - Developing an Effective CAPA Strategy
Learn deviation management and other topics we offer from certified instructors by registering for your next
CfPIE course today.
Blog Categories
Stay Informed