Medical Device Validation: Why It’s Important and What You Need to Know About It
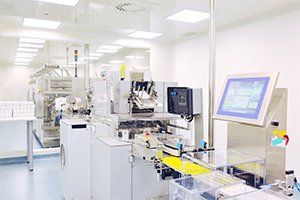
Medical device validation is the process of ensuring that the medical device being manufactured will function safely and appropriately. The standards for validation and verification are set by regional regulatory bodies as well as international standards, which often overlap when it comes to product requirements.
Every manufacturer involved in producing medical devices must receive the appropriate
medical device training. Without the appropriate training, quality assurance managers and employees may fail to properly validate the devices being produced. You can avoid this issue by ensuring that every employee in the manufacturing team has a
medical device training certificate.
We’re going to discuss medical device validation, process, testing and verification, explore common challenges faced when validating, and hone in on the importance of this entire practice when it comes to meeting quality system design specifications in the healthcare industry.
What Is Medical Device Validation?
Medical device validation is the process of ensuring that the medical device being manufactured will consistently provide the intended benefits for its use condition. Validation is usually done by a series of tests and inspections. These same practices can also apply to process validation, which ensures that the processes used to manufacture the device meets FDA guidelines when the product itself cannot be inspected.
Verification is closely related to medical device validation but is typically the process of making sure that each element used within the medical device is up to the appropriate standards. Just like with validation, tests and inspection are typically the tools used to carry out verification and to ensure product requirements and design controls are being followed.
There are a plethora of technologies, levels of complexity, and sizes of medical devices that all must be validated. The standards for validating these devices are driven by regulatory organizations and international standards. It’s important for anyone involved in validating devices to receive the appropriate
medical device validation training so that they are aware of all relevant regulations.
The Importance of Medical Device Validation in Meeting Quality System Design Specifications
The ultimate purpose of all the rules and regulations that go into medical device validation is to ensure that manufacturers are creating products that will safely be used in medical situations. Even the smallest malfunction can be life-threatening with many medical devices, making validation well worth the time and resources.
Not only will the organization be in compliance with all applicable regulations by carrying out medical device validation, but it can avoid the negative reputation that accompanies producing unsafe devices. Of course, failing to be in compliance will result in various consequences for medical device companies that will impact the business, such as heavy fines.
Challenges in Medical Device Validation
Medical device validation can be challenging due to the diverse range of devices, each with its unique functionality and intended use. Ensuring that a device performs consistently and safely in real-world scenarios requires rigorous testing and documentation. Every product quality manager should be aware of a few new hurdles that must be overcome with validation and verification during the product development process. It’s of the utmost importance that quality managers and related roles receive the appropriate medical device training.
Global Regulatory Differences
Different countries have varying regulations and standards for medical device validation. Understanding these differences is crucial for manufacturers aiming for global distribution.
Cybersecurity for Medical Devices
Medical device validation has become increasingly complex as technology has evolved. Now, many medical devices require software to function, introducing an entirely new element that must be validated. Not only must the software function as intended, but Internet-connected devices must also ensure that they have adequate cybersecurity solutions onboard.
The United States Food and Drug Administration has been aware of the need for cybersecurity for some time and has put more emphasis on security following the
2017 WannaCry ransomware attack that affected life-saving medical devices.
Medical device manufacturers that produce devices reliant on software must ensure that both the hardware and software are validated. This represents a brand new challenge that medical device manufacturers must overcome.
High-Risk Devices Must be Validated
Many medical devices can be considered high-risk as they carry the threat of severe injury or death if they malfunction. These devices are often surgical devices, but there are other types of high-risk devices, such as pacemakers, that are implanted.
High-risk devices must be thoroughly validated and verified to save lives. However, validating these devices is often challenging due to their complexity. This makes validating a high-risk device a challenge that must be resolved. On top of other quality assurance systems, validating the process of manufacturing the device will further ensure that the device will function as expected. Everyone involved with validating high-risk medical devices must take the appropriate medical device training courses.
Processes Must Be Validated If a Product Cannot Be Inspected
There are some products that cannot be reasonably validated by the usual methods. In these situations, the challenge becomes how can a manufacturer ensure that the device is operating effectively if it cannot be properly validated?
In these situations, the manufacturer must then validate the manufacturing process itself. A manufacturer must be able to provide evidence that the process they’ve employed will create a properly functioning medical device. Depending on the relevant regulations,
medical device process validation is often enough to remain in compliance.
Role of Technology in Validation
Modern technologies, such as simulation software and advanced testing equipment, play a pivotal role in streamlining the validation process. They allow for more accurate predictions of device performance under various conditions.
Overcome Challenges with Diverse Well-Trained Teams
Experts in different fields must work together to design medical devices that will easily be validated and verified. Design verification is usually the first step to occur before anything has been physically created. Teams with varied disciplines and the appropriate level of training can thoroughly examine if a design will carry out its intended purpose before a prototype is even created.
Consider all the levels of expertise that must work together when it comes to device specifications andcreating a moderately complex medical device. You will need someone with expertise in mechanical engineering, chemistry, software engineering, engineering for integrated chips, prototyping methods, and providing a great user experience. Starting out with the right team will mean that validation and verification in the future are as seamless as possible.
Training and Skill Development
Ensuring that the personnel involved in the validation process are adequately trained is crucial. This ensures that the validation process is conducted accurately and in compliance with regulatory standards.
An expert in software engineering, for example, may not be familiar with the standards in place for developing software for medical devices. The appropriate training is absolutely necessary.
CfPIE offers several courses covering Validation and Design Control for Medical Devices including:
- Medical Device Process Validation Training for Professionals
- US Medical Device Law & FDA Design Controls Essentials
- US Medical Device Regulations - Design Verification Validation & Risk Analysis
Also, you can prepare your team today by enrolling them in CfPIE’s
Certified Medical Device Compliance Professional (CMDCP) Program. Not sure what you need? Explore our wide variety of
medical device courses today.
Blog Categories
Stay Informed