Validation & Verification in GMP: Ensuring Consistency from Equipment to Final Product
Creating safe, effective products under Good Manufacturing Practices means proving every step works exactly as intended. Validation and verification provide that proof.
Keep reading to learn how equipment qualification (IQ, OQ, PQ), process validation in manufacturing, computerized systems validation, and other checks work together to ensure consistent product quality and regulatory compliance.
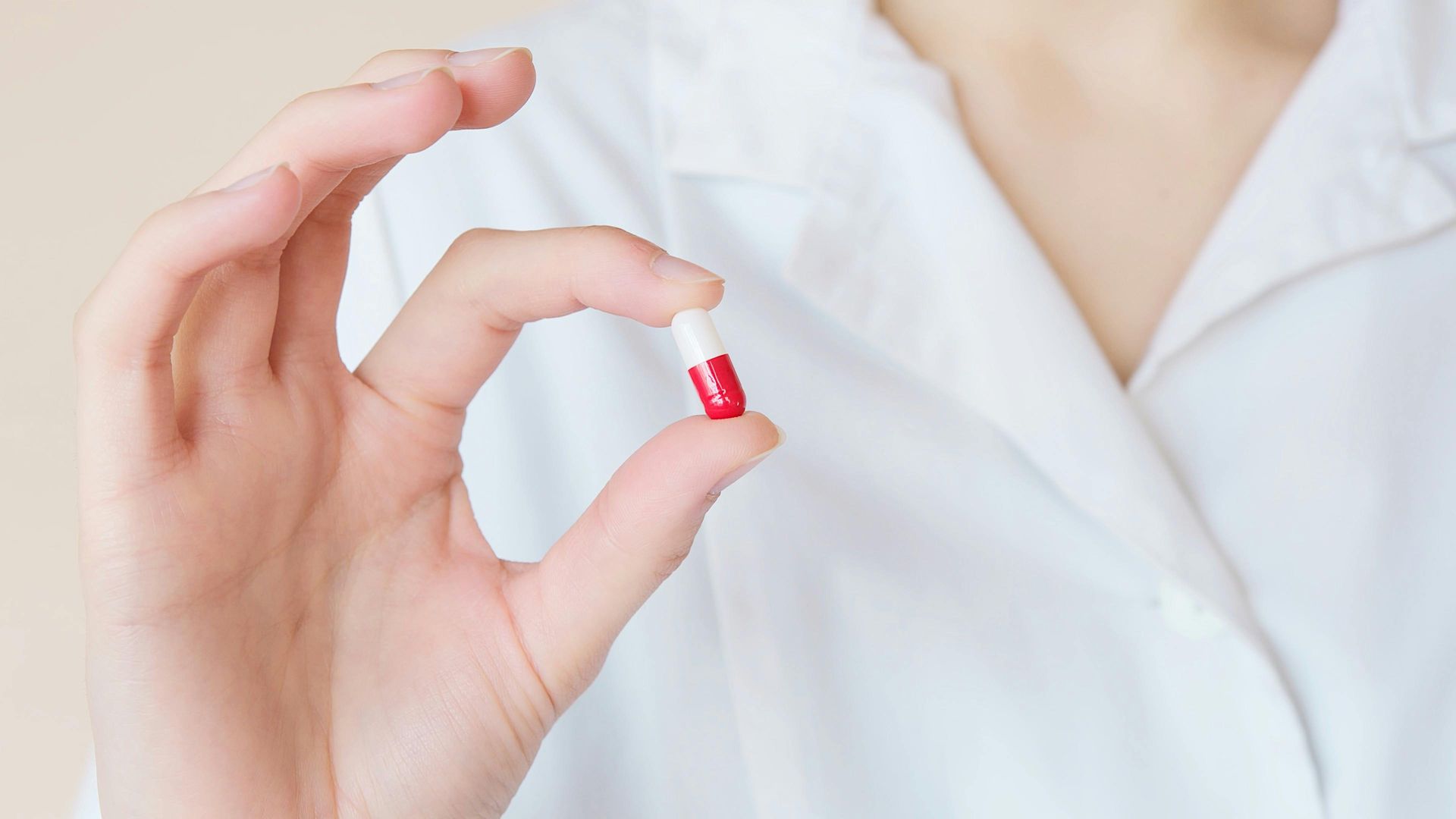
Equipment Qualification
Before you can validate a process, you must confirm the tools you’re using are adequate for the job. Equipment qualification typically includes three phases:
- Installation Qualification (IQ)
- Operational Qualification (OQ)
- Performance Qualification (PQ)
IQ confirms the equipment is installed correctly according to specifications. OQ verifies that it functions as expected under standard conditions. PQ demonstrates that the equipment performs reliably under real production scenarios.
Maintaining calibration schedules and preventive maintenance logs is just as important. Skipping these steps can jeopardize every product batch that follows.
Always keep user manuals and vendor documentation accessible to support qualification efforts. These documents often provide setup, operation, and troubleshooting details; and auditors frequently refer to them during audits.
Process Validation
Manufacturing process validation demonstrates that your production process consistently yields products meeting predetermined specifications.
Start by identifying critical process parameters (CPPs) — the variables that directly impact product quality. Then, test pilot batches or qualification runs to check for repeatability and reliability.
The work doesn’t end after initial validation. Post-validation monitoring ensures the process remains in control. Any drift or deviation from validated parameters should trigger a review to prevent quality issues downstream.
Cleaning Validation
With strict rules around contamination, cleaning validation is another non-negotiable process in GMP-regulated environments. Cleaning procedures effectively remove residue from equipment, including cleaning agents, microbial contaminants, and the product itself.
Standard techniques include swab tests and rinse samples, which help confirm cleanliness to predefined limits. Document and revalidate these procedures whenever you change the cleaning process, equipment, or materials.
Computerized Systems Validation
Modern manufacturing operations rely heavily on software and automation, which means computerizedsystems validation (CSV) is as critical as validating physical equipment. Systems must meet compliance standards such as 21 CFR Part 11, which governs data integrity in electronic records and signatures.
Companies should implement user access controls, maintain audit trails, and perform regular system backups to ensure compliance. Periodic reviews can catch software updates or configuration changes that may introduce new risks.
Verification Activities
Where validation demonstrates that a process works, verification confirms that it continues to work, batch after batch. Common verification activities include:
- In-process testing
- Final product inspections
- Batch record reviews
These steps help identify and correct problems before they impact the final product. Setting clear acceptance criteria is key to effective verification. Flag and investigate any results that fall outside the defined range.
Documentation and Change Control
Clearly record and store every protocol, result, and deviation. When something changes, like a process, piece of equipment, or raw material, update validation documents accordingly.
Change control, a process for evaluating, approving, and implementing changes, helps ensure changes don’t inadvertently compromise validated systems. If a validation failure occurs, trigger CAPA procedures (Corrective and Preventive Actions) to address the root cause and prevent recurrence.
Master GMP Systems with CfPIE’s Targeted Courses
Validation and verification build confidence in your processes, products, and people. From installation qualifications to routine checks, every element contributes to a culture of quality and control.
Looking to enhance your team’s knowledge of GMP validation and verification? CfPIE offers practical, expert-led training to help your organization navigate everything from equipment qualification, IQ, OQ, and PQ to computerized systems validation.
Blog Categories
Stay Informed