GMP Audit Pitfalls: Top Mistakes and Proactive Strategies to Prevent Them
Preparing for a GMP audit can feel like prepping for an open-book test until you realize the book is missing pages. Even minor slip-ups can lead to significant consequences, from overlooked records to forgotten training updates.
Keep reading to learn how to improve documentation, sharpen your training, and avoid GMP audit pitfalls that could cost you big.
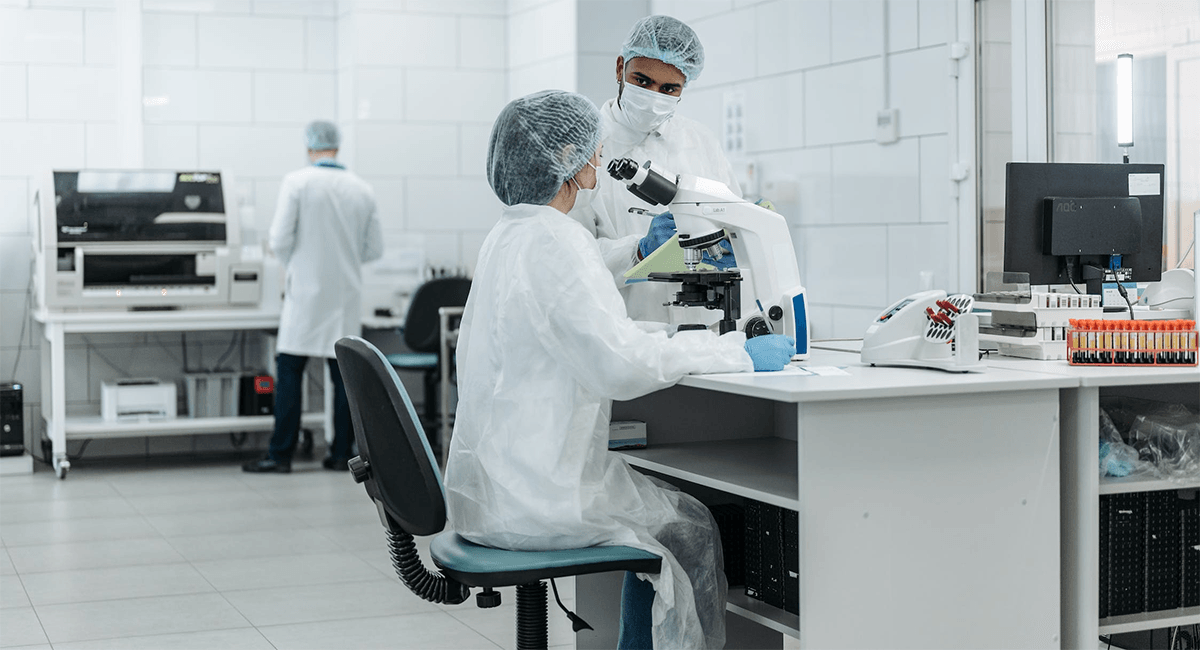
Pitfall #1: Poor Documentation Practices
Sloppy paperwork is one of the fastest ways to fail an audit. Missing signatures, incomplete batch records, or corrections with no explanation? Auditors notice these deviations right away. And when you don’t update your records in real-time, your entire system can look shaky.
The fix here is simple but powerful: lock in your GMP documentation requirements with
clear SOPs, routine checks, and a culture that values getting it right the first time.
Pitfall #2: Inadequate Training and Competency
Untrained employees can do more than slow down operations. They increase the likelihood of GMP audit pitfalls, and skipped steps or misunderstood procedures can quickly lead to GMP violations.
A strong
training program helps prevent these issues. Make sure it covers onboarding, role-specific instruction, and regular refreshers. Use simple assessments or quick check-ins to reinforce key points, and consider linking training milestones to performance reviews to keep everyone accountable.
Pitfall #3: Improper Handling of Deviations
One of the most common GMP mistakes is failing to dig into the root cause, or worse, leaving CAPAs half-finished and forgotten.
Make deviation tracking part of your team’s daily routine. Log issues as they happen and use a structured problem-solving approach to work through them. Every CAPA should have a timeline, clear ownership, and evidence that the fix worked. That kind of follow-through shows auditors you take quality seriously.
Pitfall #4: Neglecting Environmental and Cleaning Protocols
Dust, condensation, and stray particles, which might seem like minor issues, can lead to contamination risks if your cleaning protocols fail. Auditors often head straight for your environmental monitoring logs, especially in cleanroom settings.
Validated cleaning procedures, standardized checklists, and detailed frequency logs keep everything on track. Conduct spot checks to confirm staff follow procedures and train them to ensure they know how to report issues. A clean space with up-to-date records gives auditors peace of mind.
Pitfall #5: Inconsistent Change Control
Change is part of any operation, but every adjustment needs proper documentation in GMP environments. Updating a process or switching out equipment without approval, even with good intentions, can result in major non-conformances if there’s no clear record of what was done and why.
Avoid that risk with a
formal change control process. Every modification, whether to a material, equipment, or process flow, should include an impact assessment, approval sign-offs, and a post-implementation review.
Preparing For Audits: Action Steps
Once your core quality systems, such as training programs, documentation controls, deviation tracking, and change management, are running smoothly, focus on these audit readiness tips:
- Schedule mock audits and walkthroughs that use actual checklists and scenarios. Do more than rehearse responses; let your team practice locating records, explaining procedures, and answering questions.
- Bring in external experts if you’re expanding into new markets, adjusting your QMS, or preparing for a high-stakes inspection. Their outside perspective can help uncover blind spots.
- Keep all records easy to access, up to date, and organized by category so there’s no last-minute scramble. When everything's in place, your team can approach audits with confidence, not anxiety.
Avoiding GMP Non-Compliance Starts With Preparation
GMP audits don’t have to be stressful or unpredictable, especially when you've invested in systems that support daily compliance and long-term growth.
With training from CfPIE, your team can avoid GMP audit pitfalls, improve daily processes, and stay ready for anything that comes your way.
Blog Categories
Stay Informed