Quality Assurance vs. Quality Control in the Pharmaceutical Industry
When people’s health and lives are on the line, pharmaceutical companies should spare no expense in providing due diligence over their own drug and medical device manufacturing lines. Checking for defects in the finished product matters even more when the stakes are this high, hence the need for quality assurance (QA) and quality control (QC).
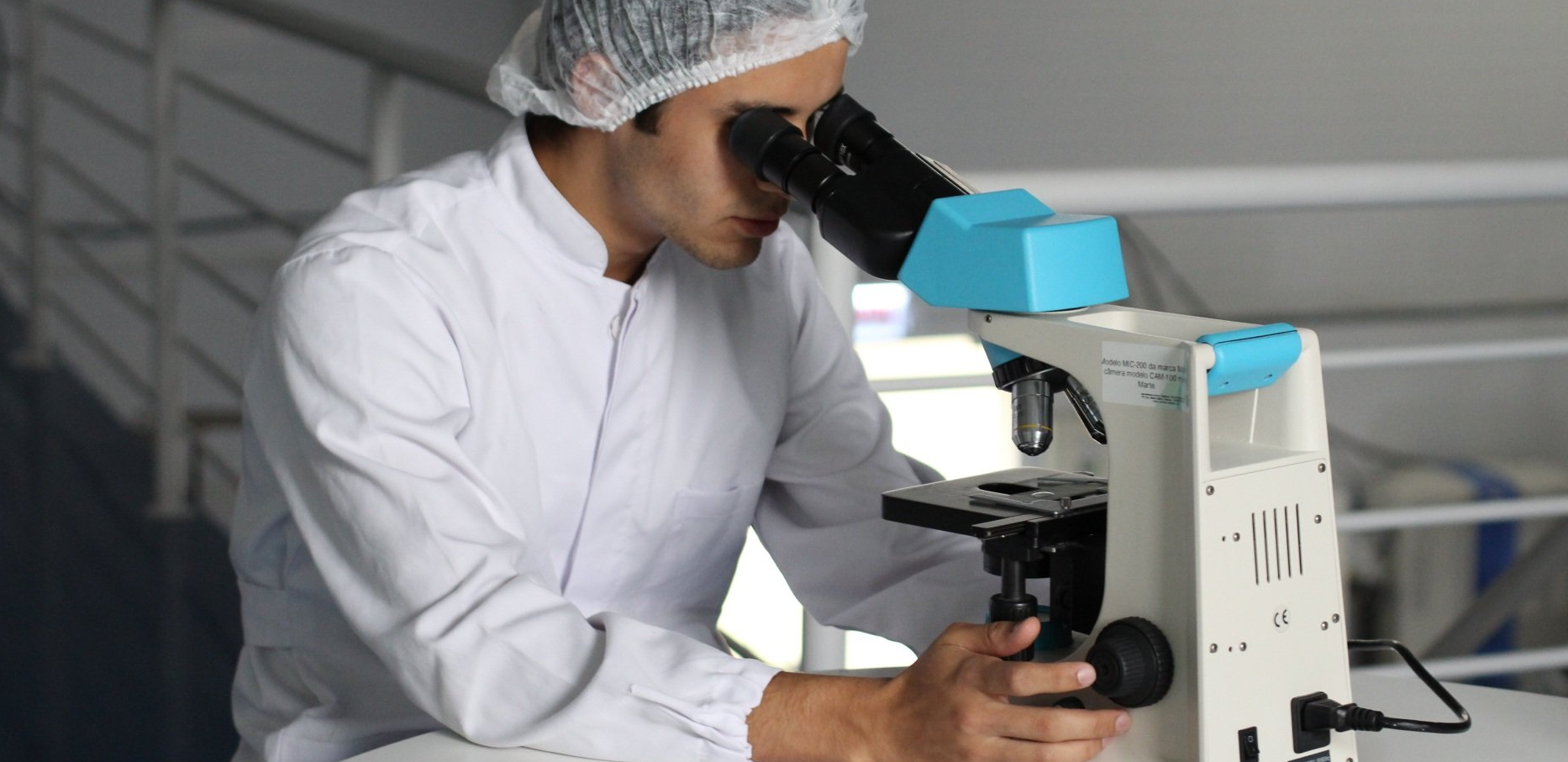
Both procedures help medical companies and pharmaceutical manufacturers improve their product quality, conduct risk management and mitigation, and better follow regulatory requirements and standards. Both are essential if you work with quality management system (QMS) for a company in the biotechnology or pharmaceutical manufacturing fields. You can also reference our previous blog post on the importance of pharmaceutical quality assurance. Read it here
First, let’s discuss the differences between quality assurance and quality control. What’s the subtle yet key difference between the two procedures, and how do you gain their benefits as a pharmaceutical or medical device manufacturing organization?
What Is Quality Assurance and Quality Control?
The official definitions for QA and QC can be found on the ISO standards website, but here we will dig deeper into the precise differences between the two.
Quality assurance ensures that the final product coming out of the production line is both safe and effective. Whether it’s a medicine or a medical device, the effects of its use must be intended or at least expected. Quality assurance activities are directly integrated into the manufacturing process.
Quality control activities revolve around the set of procedures used to check and verify that a final product meets pre-established quality standards.
Together, both play a vital role in ensuring your organization is following best practices on the way to becoming compliant with relevant regulatory agencies like the FDA.
What Is the Relationship Between QA and QC in the Pharmaceutical Industry?
Both terms sound similar, are necessary for an overall quality management system, and are often used interchangeably, but the important differences between QA and QC are:
- Timing: QA aims to take a proactive stance by focusing on preventive actions to minimize and eliminate defects before they occur during manufacturing, while QC, which is more reactive, identifies possible quality issues after the fact and verifies the quality of the output.
- Duration: QA is a long-term process that covers the entire development cycle, while QC is more short-term and happens at the end of the manufacturing process during the testing phase.
- Steps: QA may involve producing detailed documentation, processing audit checklists, and supplier management. QC covers product sampling, testing, and inspections of raw material, products, devices, etc.
- Responsibility: All life science manufacturing companies should aim to establish a culture of quality in their organizations. Everyone should be involved in quality assurance efforts. And while quality control is just as important, most companies designate the responsibility to a dedicated QC department.
Every manufacturer in the medical field practices both processes rigorously in order to conform to the high standards of the industry.
How Do I Learn Quality Assurance and Quality Control?
The only question left to answer now is “How do I instill QA and QC principles in my organization and start reaping the benefits?”. Quality assurance training courses are now available, and they can be useful for boosting various aspects of quality management.
- Quality risk management: The potential for defects can never be fully eliminated, but proper quality training can be used to keep those risks low while making the benefits worthwhile.
- Compliance: Healthcare regulations are notoriously stringent such as Good Manufacturing Practices followed by drug and medical device manufacturers. Training will ensure you stay compliant by calibrating equipment properly, keeping detailed documentation, and generally improving QA and QC testing.
- Brand trust and reputation: Customers are more likely to work with you when they know that their health is in good hands. Implementing QA and QC training is an excellent way to demonstrate your dedication to safety standards and maintain the level of quality your customers expect.
- Skill development: Providing coursework for your personnel makes them more proficient at their jobs, thereby strengthening your quality management program. Experienced staff are better at checking for errors, conducting comprehensive audits, and investigating issues.
Training is also a way to demonstrate legal compliance through certification programs and, as medical findings and standards change, even experienced staff will still need a refresher course now and again.
Getting Your QA and QC Training From the Right Place
The benefits you get from QA and QC training greatly depend on where you’re getting it from. Regardless, any organization operating in the pharmaceutical, medical device, cosmetics, and other life science industries must have effective QA and QC processes in place.
For industry-grade coursework taught by certified professionals in the field, be sure to check out Quality Assurance/Quality Control for Biologics and Biopharmaceuticals.
Quality assurance and quality control specialists can’t afford to miss this opportunity and may also be interested in exploring other on-site and virtual programs offered by CfPIE.
Blog Categories
Stay Informed